Avoiding errors on machine-tools is essential if the dimensional quality of the parts made on them is to be assured and the financial losses caused by faulty parts are to be avoided. Machine-tools are therefore checked by means of geometrical tests to determine positioning and trajectory errors so that any errors can be corrected.
MH-CHECK is an innovative system that seeks to take metrology to the next level and offer a fast, reliable solution to machine-tool checking needs. Its main characteristics are explained below.
The MH-CHECK system is made to enable the status of machine-tools to be checked quickly. Checking is performed by a self-centring head that measures a standard artefact (pattern sphere cubes, tetrahedrons and bars) and then uses calculation software to identify errors in position, perpendicularity and length in space on the machine-tool. The check takes about 10 minutes, which makes it significantly faster than other techniques.
The purpose of the MH-CHECK system is to increase the quality of the parts manufactured. It does this by running regular checks to identify machine-tool errors.
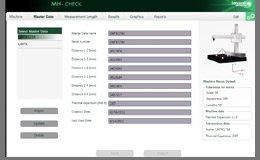
Advantages:
MH-CHECK Feel Gauge
The MH-CHECK feel-gauge is a high-precision, self-centring feel gauge comprising three high-precision longitudinal meters that contact the pattern spheres of the artefact. The sensors recognise the centres of the spheres fully automatically by reading the linear displacement of each actuator and running internal calculations with their software. It is essential to have extremely accurate calculations in this system for the feel gauge to be able to locate the centres of the pattern spheres even if the displacement of the longitudinal sensors is different in each measurement, and thus obtain a constant, highly repeatable home point (initial coordinates X,Y,Z – (0, 0 ,0)) for checking the machine-tool.
Apart from the special design of the feel gauge, the system also stands out for the incorporation of a laser to facilitate gauge location in space and speed up the process to ensure that contact with each sphere is fast and precise.
General characteristics:
Pattern sphere tetrahedron
The star artefact of the MH-CHECK is a tetrahedron with ceramic spheres, which is measured via a self-centring feel gauge. Once the measurements taken by the machine-tool are obtained, they can be compared with the readings taken by the tetrahedron pattern artefact to check for errors in position, perpendicularity and length. These can be measured thanks to the structure of the artefact.
General characteristics:

Depending on the type of machine-tool on which the artefact is used, 2 different sizes of tetrahedron are available to increase the field of application and scope for use of the system.
Software
The MH-CHECK system has software created specifically for machine-tools and coordinate measuring machines. This software, which is compatible with Microsoft® Windows®, handles the general analysis of the system and interprets the state of each feel gauge so as to run the calculations required and show the geometrical errors in the equipment to be checked.
MH-CHECK software is a high graphic in its format, and easy to use, making the system highly intuitive. It has the following characteristics.